


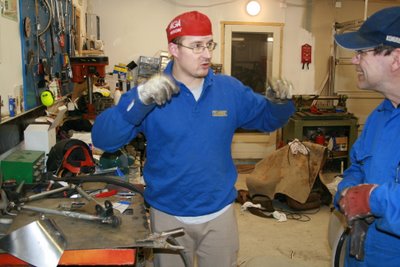

Our story about building and racing two Yamaha R1 powered Locosts in Finland.
We will have 60mm wider a-arms compared to PMC:s jigtable that we borrowed, so sadly it was of no use for us (they didn't really believe we had this much wider suspension). We still had to make it a bit of a compromise because we weren't sure which brake parts and wheels we would use. With the Taunus stock calipers we could have still gone ~35mm wider. Our racing rules state that the suspension has to be under 1660mm wide, so we would like to make use of all the space allowed.
A picture of our jigtable, it is for both front a-arms.
We got the upper front a-arms sorted out too, they just need to be welded together. So the front end is looking quite good at the moment, all it need is to be welded together.
We also tested brake options, seems like we can never get the brakes to fit into 13" wheels, so I guess we'll have to step up to 15...
No way. The brake disc is as big as the 13" wheel. Brake disc is from a GT3 Porsche and the caliper is from a Cayenne.
And some results. One nosecone for each car, plus one as a spare when something happens.
The mold for the seat, borrowed from our school's formula student.